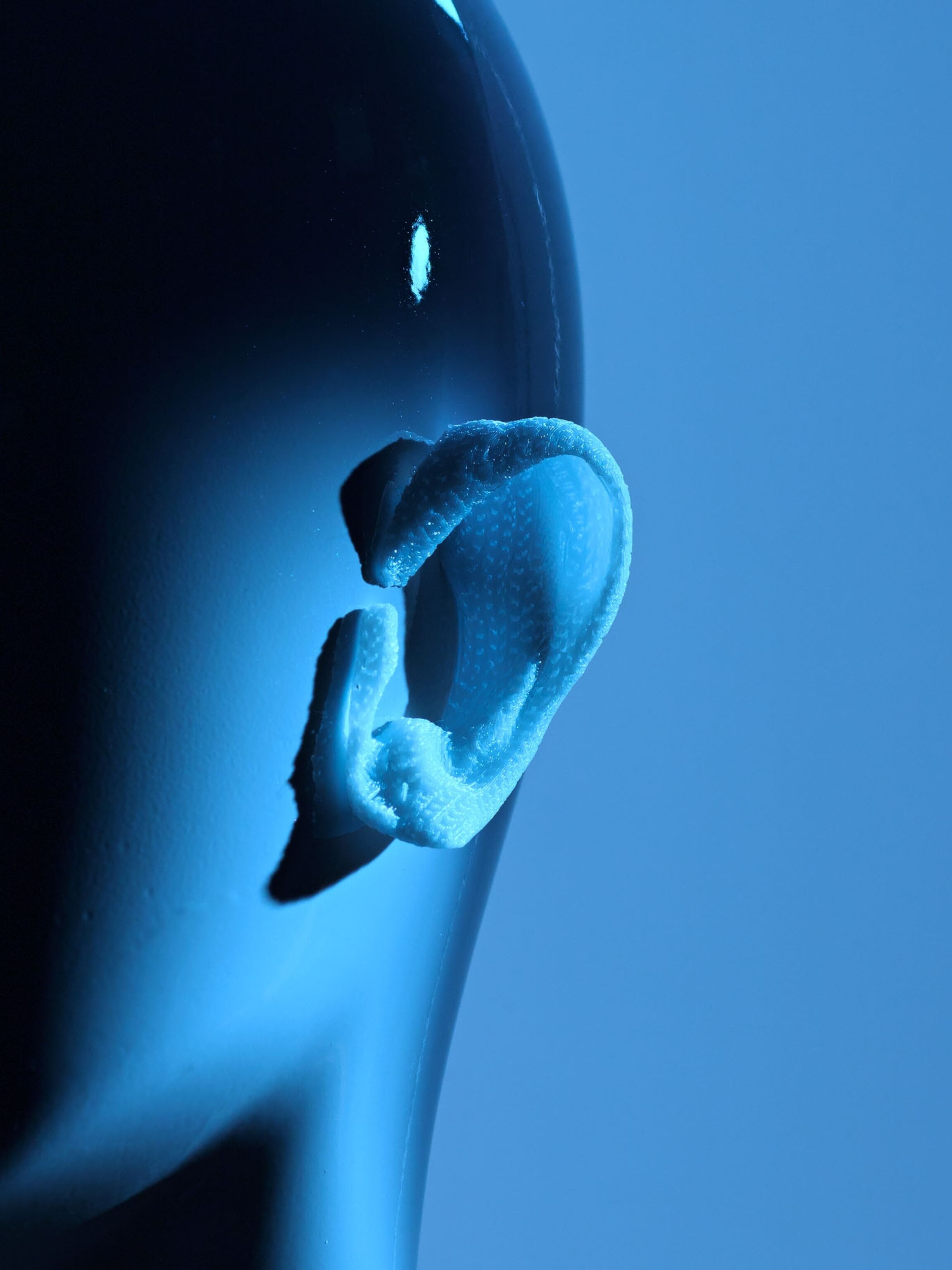
Scientists Use 3-D Printers to Make Body Parts
Human cells are the ink.
What if you could press a button and a machine would make you a new nose or kidney? Scientists are exploring that futuristic vision by using special 3-D printers to make living body parts.
Called bioprinters, these machines use human cells as “ink.” A standard 3-D printer layers plastic to create car parts, for example, or trinkets, but a bioprinter layers cells to form three-dimensional tissues and organs.
To create an ear, the printer lays down a pliable, porous scaffold made of hydrogel, a kind of polymer. The scaffold is covered with skin cells and cartilage cells, which grow and fill in the ear-shaped form. The hydrogel eventually biodegrades; after about six months the ear is composed entirely of human cells. “We use the patient’s own cells,” says Anthony Atala, director of Wake Forest University’s Institute for Regenerative Medicine. That way the organs won’t be rejected.
Before programming a machine to build a body part, Atala says, scientists need to figure out how to create it themselves. In their labs they have grown bladders, blood vessels, and many other anatomical parts that have been implanted into patients.
Now they’re translating them for 3-D bioprinters and hope to soon be able to implant printed organs too. Already miniature kidneys and livers are used to test drugs, including chemotherapy agents.
Is there any area of anatomy that can’t be made in this way? Printing at least parts of the human heart should be possible, Atala says. What about the brain? “Definitely not in my lifetime!”
Related Topics
Go Further
Animals
- This ‘saber-toothed’ salmon wasn’t quite what we thoughtThis ‘saber-toothed’ salmon wasn’t quite what we thought
- Why this rhino-zebra friendship makes perfect senseWhy this rhino-zebra friendship makes perfect sense
- When did bioluminescence evolve? It’s older than we thought.When did bioluminescence evolve? It’s older than we thought.
- Soy, skim … spider. Are any of these technically milk?Soy, skim … spider. Are any of these technically milk?
- This pristine piece of the Amazon shows nature’s resilienceThis pristine piece of the Amazon shows nature’s resilience
Environment
- This pristine piece of the Amazon shows nature’s resilienceThis pristine piece of the Amazon shows nature’s resilience
- Listen to 30 years of climate change transformed into haunting musicListen to 30 years of climate change transformed into haunting music
- This ancient society tried to stop El Niño—with child sacrificeThis ancient society tried to stop El Niño—with child sacrifice
- U.S. plans to clean its drinking water. What does that mean?U.S. plans to clean its drinking water. What does that mean?
History & Culture
- Meet the original members of the tortured poets departmentMeet the original members of the tortured poets department
- Séances at the White House? Why these first ladies turned to the occultSéances at the White House? Why these first ladies turned to the occult
- Gambling is everywhere now. When is that a problem?Gambling is everywhere now. When is that a problem?
- Beauty is pain—at least it was in 17th-century SpainBeauty is pain—at least it was in 17th-century Spain
- The real spies who inspired ‘The Ministry of Ungentlemanly Warfare’The real spies who inspired ‘The Ministry of Ungentlemanly Warfare’
Science
- Here's how astronomers found one of the rarest phenomenons in spaceHere's how astronomers found one of the rarest phenomenons in space
- Not an extrovert or introvert? There’s a word for that.Not an extrovert or introvert? There’s a word for that.
- NASA has a plan to clean up space junk—but is going green enough?NASA has a plan to clean up space junk—but is going green enough?
- Soy, skim … spider. Are any of these technically milk?Soy, skim … spider. Are any of these technically milk?
- Can aspirin help protect against colorectal cancers?Can aspirin help protect against colorectal cancers?
Travel
- What it's like to hike the Camino del Mayab in MexicoWhat it's like to hike the Camino del Mayab in Mexico
- Is this small English town Yorkshire's culinary capital?Is this small English town Yorkshire's culinary capital?
- This chef is taking Indian cuisine in a bold new directionThis chef is taking Indian cuisine in a bold new direction
- Follow in the footsteps of Robin Hood in Sherwood ForestFollow in the footsteps of Robin Hood in Sherwood Forest